Building Effective Manufacturing Skills Management Programs
A comprehensive guide to implementation
In todays rapidly evolving manufacturing landscape, implementing an effective skills management program requires a structured approach. A well-designed skills management system not only improves operational efficiency but also enhances employee engagement and career growth opportunities. This guide walks through five essential steps to create and maintain a successful skills management system that benefits both your workforce and business outcomes.
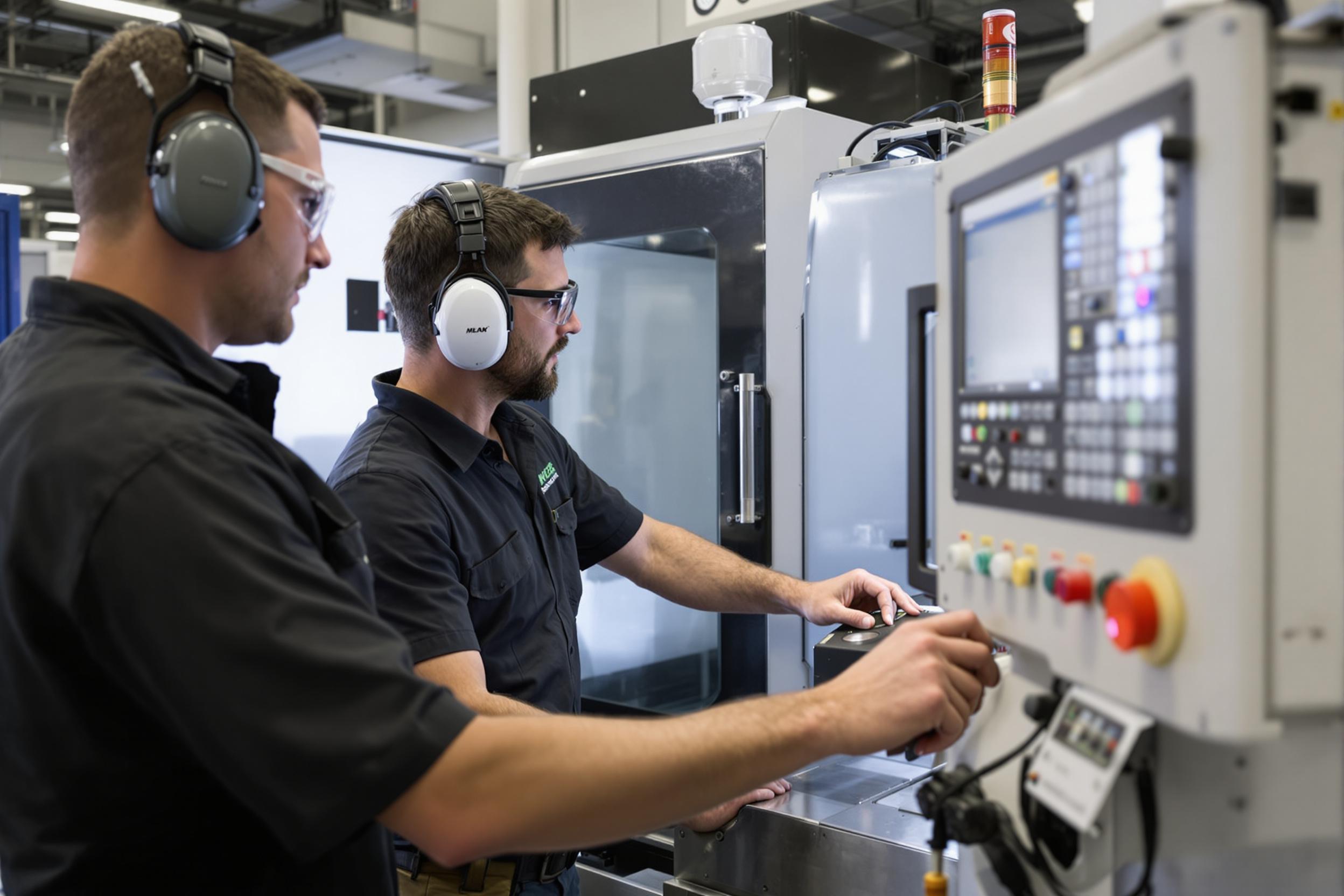
1. Define Clear Role Structures
Clear role structures are the foundation of effective skills management. When employees understand their current role requirements and see a clear path forward, they're more likely to engage in skill development and remain with the organization long-term.
Role Standardization
Inconsistent job titles and unclear progression paths create confusion and frustration. For instance, having one department call a position 'Machine Operator Level 2' while another uses 'Senior Equipment Technician' for the same role makes it difficult to:
- Compare skills across departments
- Create standardized training programs
- Establish clear career advancement paths
- Ensure fair compensation practices
In CNC operations, a standardized progression might include:
- CNC Operator I
- CNC Operator II
- CNC Operator III
- Lead CNC Machine Operator
This clear structure helps employees understand their next career step and what they need to do to advance.
Skill Categories
Within each standardized role, clearly defined skill requirements set expectations for both current performance and future advancement. Breaking skills into technical and soft categories helps employees understand the full scope of their role beyond just technical operations.
These skill requirements serve multiple purposes:
- Provide clear performance expectations
- Guide training program development
- Support fair performance evaluations
- Enable targeted skill development
2. Establish Baseline Skill Requirements
Understanding current workforce capabilities versus role requirements helps identify gaps and opportunities for both individual growth and organizational improvement.
Role-Specific Requirements
Skills should build progressively through role levels, with each level maintaining fundamental skills while adding complexity and responsibility. This approach:
- Creates clear development paths
- Ensures foundational skills arent lost
- Supports consistent quality
- Enables effective cross-training
3. Create Training Pathways
With clear roles and skill requirements established, structured training pathways provide the roadmap for employee development. Well-designed training paths benefit both employees and the organization by:
- Accelerating skill development
- Reducing training costs
- Improving employee retention
- Ensuring consistent skill acquisition
4. Implementing Assessment Programs
Regular skill assessment isnt just about checking boxes – its about ensuring operational excellence and identifying opportunities for improvement. A strong assessment program:
- Validates training effectiveness
- Identifies emerging skill gaps
- Supports succession planning
- Ensures regulatory compliance
5. Documentation and Management Systems
While many organizations start with spreadsheets, this approach quickly becomes unmanageable as workforce size and skill complexity grow. Modern skills management software provides comprehensive solutions that streamline the entire process.
Conclusion
Successful manufacturing skills management programs require dedication, proper tools, and consistent execution. By following these five key steps and leveraging modern solutions, organizations can create a more skilled, adaptable, and productive workforce while improving operational efficiency and employee satisfaction.
Share this article
Related Posts

Learn how skill matrices help manufacturing organizations track and develop employee capabilities effectively.
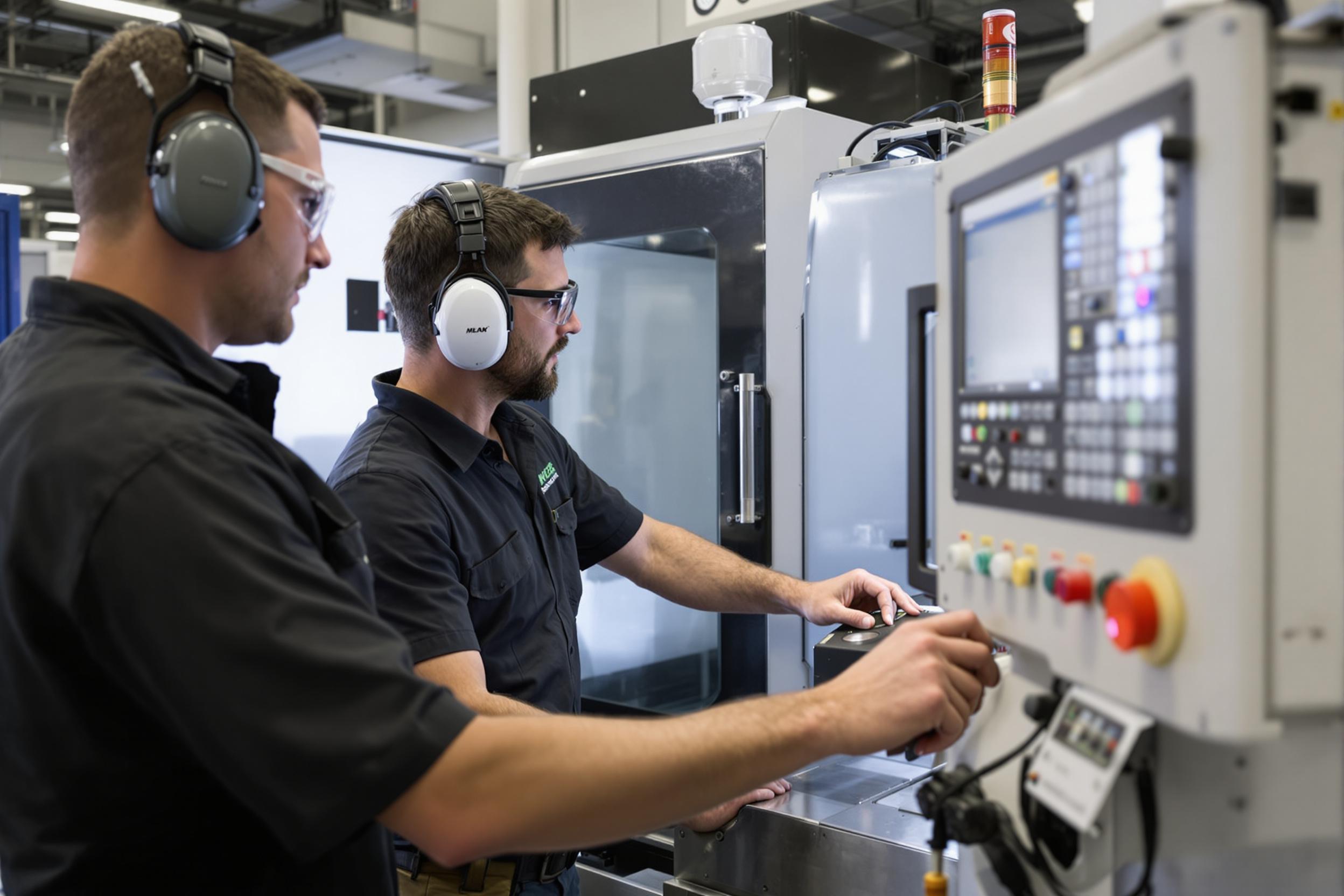
Discover how precision machine shops are leveraging skill management to maintain quality and efficiency.